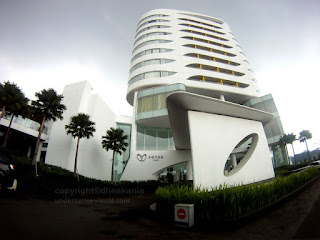
Jenis material konstruksi yang digunakan untuk membangun Sensa Hotel kurang lebih sama dengan material yang biasa dipakai untuk membangun sebuah bangunan, yaitu beton, beton bertulang, baja, semen, pasir, batu bata, kaca, WPC, dan lain-lain. Proporsi tiap materialnya sebagai berikut
1. Beton 20%
2. Beton bertulang 18%
3. Batu bata 20%
4. Pasir 8%
5. Semen 8%
6. Baja 17%
7. Kaca 7%
1. Pada tahap perencanaan kita buat gambar desain bangunan untuk menggambarkan bentuk konstruksinya dan menentukan letak kolom struktur.
2. Selanjutnya melakukan perhitungan struktur bangunan untuk mendapatkan dimensi kolom dan bahan bangunan yang kuat untuk digunakan namun tetap ekonomis.
3. Melakukan pekerjaan pengukuran untuk menentukan posisi kolom bangunan, ini harus pas sesuai dengan gambar rencana. apalagi pada gedung bertingkat tinggi yang angka toleransi kesalahan hanya beriksar 1 cm, jika salah dalam mengukur maka ada resiko keruntuhan gedung.
4. Menghitung kebutuhan besi tulangan dan bentuk potongan besi yang perlu dipersiapkan. ini sering disebut sebagai bestek besi.
5. Merangkai potongan besi sesuai dengan bentuk kolom yang telah direncanakan.
6. Memasang rangkaian besi tulangan pada lokasi kolom yang akan dibuat.
7. Membuat bekisting / cetakan. bisa terbuat dari kayu, plat alumunium atau media lain yang mampu menahan saat proses pekerjaan pengecoran beton.
8. Memasang bekisting sehingga membungkus besi tulangan.
9. Melakukan pengecekan posisi bekisting apakah sudah sesuai dengan ukuran rencana, dan apakah sudah benar-benar tegak.
10. Menghitung kebutuhan beton yang dibutuhkan.
11. Membuat adukan beton atau memesan beton precast dengan kualitas sesuai hasil perhitungan semula. misalnya mau menggunakan mutu beton K-250, K-300, K-400 dan seterusnya.
12. Melakukan pekerjaan pengecoran kolom, penentuan tinggi cor bisa dilakukan dengan berpedoman pada ukuran bekisting atau mengukur sisa cor dari ujung atas bekisting.
7. Kaca 7%
1. Pada tahap perencanaan kita buat gambar desain bangunan untuk menggambarkan bentuk konstruksinya dan menentukan letak kolom struktur.
2. Selanjutnya melakukan perhitungan struktur bangunan untuk mendapatkan dimensi kolom dan bahan bangunan yang kuat untuk digunakan namun tetap ekonomis.
3. Melakukan pekerjaan pengukuran untuk menentukan posisi kolom bangunan, ini harus pas sesuai dengan gambar rencana. apalagi pada gedung bertingkat tinggi yang angka toleransi kesalahan hanya beriksar 1 cm, jika salah dalam mengukur maka ada resiko keruntuhan gedung.
4. Menghitung kebutuhan besi tulangan dan bentuk potongan besi yang perlu dipersiapkan. ini sering disebut sebagai bestek besi.
5. Merangkai potongan besi sesuai dengan bentuk kolom yang telah direncanakan.
6. Memasang rangkaian besi tulangan pada lokasi kolom yang akan dibuat.
7. Membuat bekisting / cetakan. bisa terbuat dari kayu, plat alumunium atau media lain yang mampu menahan saat proses pekerjaan pengecoran beton.
8. Memasang bekisting sehingga membungkus besi tulangan.
9. Melakukan pengecekan posisi bekisting apakah sudah sesuai dengan ukuran rencana, dan apakah sudah benar-benar tegak.
10. Menghitung kebutuhan beton yang dibutuhkan.
11. Membuat adukan beton atau memesan beton precast dengan kualitas sesuai hasil perhitungan semula. misalnya mau menggunakan mutu beton K-250, K-300, K-400 dan seterusnya.
12. Melakukan pekerjaan pengecoran kolom, penentuan tinggi cor bisa dilakukan dengan berpedoman pada ukuran bekisting atau mengukur sisa cor dari ujung atas bekisting.
Proses Pembuatan Kaca
Bahan baku dari industri umum kaca adalah (Austin, dkk. 2005) :
· Pasir
Pasir yang digunakan dalam membuat kaca adalah kuarsa yang sangat murni. Kandungan besi dalam pasir kuarsa ini tidak boleh melebihi 0,45% untuk barang gelas pecah belah atau 0,015% untuk kaca optik, sebab kandungan besi ini bersifat merupakan warna kaca pada umumnya.
· Soda
Soda ini berumus kimia Na2O, yang didapatkan dalam soda abu padat (Na2CO3). Sumber lainnya adalah dari bikarbonat, kerak garam dan natrium nitrat.
· Feldspar
Feldspar mempunyai rumus umum P2O.Al2O3.6SiO2, dimana R2O dapat berupa Na2O atau K2O atau campuran keduanya. Sebagai sumber Al2O3, feldspar mempunyai banyak keunggulan dibanding produk lain, karena murah, murni dan dapat dilebur dan seluruhnya terdiri dari oksida pembentuk kaca. Al2O3 sendiri digunakan hanya bila biaya tidak merupakan masalah. Feldspar juga merupakan sumber Na2O atau K2O dan SiO2. Kandungan aluminanya dapat menurunkan titik cair kaca dan memperlamba terjadinya devitrifikasi.
· Borax
Borax adalah perawis tambahan yang menambahkan Na2O dan boron oksida kepada kaca. Walaupun jarang dipakai dalam kaca jendela atau kaca lembaran, boraks sekarang banyak digunakan di dalam bernagai jenis kaca pengemas. Ada pula kaca borax berindeks tinggi yang mempunyai nilai dispersi lebih rendah dan indeks refraksi lebih tinggi dari semua kaca yang dikenal. Kaca ini telah banyak digunkan sebgai kaca optik. Di samping daya fluksnya yang kuat, borax tidak saja bersifat menurunkan sifat ekspansi tetapi juga meningkatkan ketahanna terhadap aksi kimia. borax digunakan dalam tumpak yang memerlukan hanya sedikit alkali. Harganya hampir dua kali boraks.
· Kerak garam
Istilah asingnya adalah salt cakeyang digunakan sebagai perawis tambahan pada pembuatan kaca, demikian juga beberapa sulfat lain seperti amonium sulfat dan barium sulfat dan sering ditentukan pada segala jenis kaca. Kerak garam ini dapat membersihkan buih yang mengganggu pada tanur tangki. Sulfat ini harus dipakai bersama karbon agar tereduksi menjadi sulfit. Arsen trioksidadapat pula ditambahkan untuk menghilangkan gelombang-gelombang dalam kaca.
· Kulet
Kulet adalah kaca hancuran yang dikumpulkan dari barang-barang rusak, pecahan beling dan berbagai kaca limbah. Bahan ini dapat membantu pencairan selain juga sebagai bahan untuk dasar pengolahan limbah. Bahan ini dapat dipakai 10-80% dari muatan bahan baku.
· Blok refraktori
Langkah-Langkah Umum Pembuatan Kaca
Urutan proses pembuatan kaca pada umumnya dapat digolongkan menjadi 10 langkah (Austin, dkk. 2005), yaitu:
1. transportasi bahan baku ke pabrik
2. pengaturan ukuran bahan baku
3. penimbunan bahan baku
4. pengangkutan, penimbangan dan pencampuran bahan baku dan pemuatannya ke tanur kaca
5. pengolahan bahan bakar untuk mencapai suhu yang diperlukan bagi pembentukkan kaca
6. reaksi pembentukkan kaca di dalam tanur
7. penghematan kalor melalui regenarasi dan rekuparasi
8. pembuatan bentuk produk kaca
9. penyaringan produk kaca
10. penyelesaian produk kaca
Cara Pembuatan Kaca
a. Peleburan
Tanur kaca dapat diklasifikasi sebagai tanur periuk atau tanur tangki. Tanur periuk (pot furnace), dengan kapasitas sekitar 2 t atau kurang dapat digunakan secara menguntungkan untuk membuat kaca khusus dalam jumlah kecil di mana tumpak cair itu harus dilindungi terhadap hasil pembakaran. Tanur ini digunakan terutama dalam pembuatan kaca optic dan kaca seni melalui proses cetak. Periuknya sebetulnya ialah suatu cawan yang terbuat dari lempung pilihan atau platina. Sulit sekali melebur kaca di dalam bejana ini tanpa produknya terkontaminasi atau tanpa sebagian bejana itu sendiri meleleh, kecuali bila bejana itu terbuat dari platina. Dalam tanur tangki (tank furnace), bahan tumpak itu dimuat ke satu ujung suatu “tangki” besar yang terbuat dari blok-blok refraktor, diantaranya ada yang ukuran 38 x 9 x 1.5 m dengan kapasitas kaca cair sebesar 1350 t. kaca itu membentuk kolam didasar tanur itu, sedang nyala api menjilat berganti dari satu sisi ke sisi lain. Kaca “halusan” (fined glass) dikerjakan dari ujung lain tangki itu, operasinya kontinu. Dalam tanur jenis ini, sebagaimana juga dalam tangki periuk, dindingnya mengalami korosi karena kaca panas. Kualitas kaca dan umur tangki bergantung pada kualitas blok konstruksi. Karena itu, perhatian biasanya ditujukan pada refraktori tanur kaca. Tanur tangki kecil disebut tangki harian (day tank)dan berisi persediaan kaca cair untuk satu hari sebanyak 1 t sampai 10 t. tangki ini dipanasi secara elektrotermal atau dengan gas.
Gambar 1. Diagram alir pembuatan kaca lembaran (Austin, dkk. 2005)
Tanur-tanur yang disebutkan diatas adalah tergolong tanur regenarasi (regenerative furnace)dan beroperasi dalam dua siklusdengan dua perangkat ruang berisi susunan bata rongga. Gas nyala setelah memberikan sebagian kalornya pada waktu melalui tanur berisi kaca cair, mengalir ke bawah melalui satu perangkat ruang yang diisi penuh dengan pasangan batu terbuka atau batu rongga (checkerwork). Sebagian besar dari kandungan kalor sensibel gas keluar dari situ, dan isian itu mencapai suhu yang berkisar antar 1500°C didekat tanur 650C di dekat pintu keluar. Bersamaan dengan itu, udara dipanaskan dengan melewatkannya melalui lubang regenerasi yang telah dipanaskan sebelumnya dan dicampur dengan gas bahan bakar yang terbakar, sehingga suhu nyalanya menjadi menjadi lebih tinggi lagi (dibandingkan dengan jika udara tidak dipanaskan terlebih dahulu). Pada selang waktu yang teratur, yaitu antara 20 sampai 30 menit, alirancampuran udara bahan bakar, atau siklus itu dibalik, dan sekarang masuk tanur dari ujung yang berlawanan melalui isian yang telah mendapat pemanasan sebelumnya, kemudian melalui isian semula, dan mencapai suhu yang lebih tinggi.
Suhu tanur yang baru mulai berproduksi hanya dapat dinaikkan sedikit demi sedikit setiap hari, bergantung kepada kemampuan refraktorinya menampung ekspansi. Bila tanur regenarasi itu sudah dipanaskan, suhunya harus dipertahankan sekurang-kurangnya 1200°C setiap waktu. Kebanyakan kalor hilang dari tanur melalui radiasi, dan hanya sebagian kecil yang termanfaatkan untuk pencairan. Tanpa membiarkan dindingnya mendingin sedikit karena radiasi, suhu akan menjadi terlalu tinggi sehingga kaca cair itu dapat menyerang dinding dan melarutkannya. Untuk mengurangi aksi kaca cair, pada dinding tanur kadang-kadang dipasang pipa air pendingin.
b. Pencetakan
Kaca dapat dibentuk dengan mesin atau dengan cetak tangan. Faktor yang terpenting yang harus diperhatikan dalam cetak mesin (machine molding) ialah bahwa rancang mesin itu haruslah sedemikian rupa sehingga pencetakan barang kaca dapat diselesaikan dalam tempo beberapa detik saja. Dalam waktu yang sangat singkat ini kaca berubah dari zat cair viskos menjadi zat padat bening. Jadi, jelas sekali bahwa masalah rancang yang harus diselesaikan, seperti aliran kalor stabilitas logam, dan jarak bebas bantalan merupakan masalah yang rumit sekali. Keberhasilan mesin cetak kaca merupakan prestasi besar bagi para insinyur kaca.
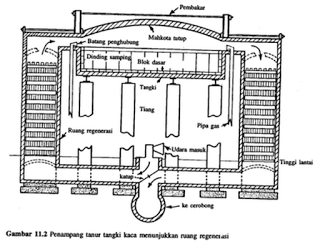
c. Penyangaian
Untuk mengurangi regangan-regangan dalam kaca, semua barang kaca harus disangai (anneal), baik barang kaca yang dibuat dengan mesin maupun yang dibuat dengan tangan. Secara singkat, penyangaian menyangkut dua macam operasi, yaitu:
1. Menahan kaca itu pada suatu suhu di atas suhu krisis tertentu selama beberapa waktu yang cukup lama sehingga mengurangi regangan-regangan dalam dengan jalan pengaliran plastic sehingga regangannya kurang dari suatu maksimum yang ditentukan.
2. Mendinginkan massa kaca sampai suhu kamar secara cukup perlahan sehingga regangan itu selalu berada di bawah batas maksimum leher atau tungku penyaringan, tidak lain hanyalah satu ruang pemanasan yang dirancang dengan baik dimana laju pendingin dapat diatur sehingga memenuhi persyaratan.
d. Penyelesaian
Semua kaca yang sudah disangai harus mengalami operasi penyelesaian yang relative sederhana tetapi sangat penting. Operasi ini menyangkut hal-hal sebagai berikut:
Untuk mengurangi regangan-regangan dalam kaca, semua barang kaca harus disangai (anneal), baik barang kaca yang dibuat dengan mesin maupun yang dibuat dengan tangan. Secara singkat, penyangaian menyangkut dua macam operasi, yaitu:
1. Menahan kaca itu pada suatu suhu di atas suhu krisis tertentu selama beberapa waktu yang cukup lama sehingga mengurangi regangan-regangan dalam dengan jalan pengaliran plastic sehingga regangannya kurang dari suatu maksimum yang ditentukan.
2. Mendinginkan massa kaca sampai suhu kamar secara cukup perlahan sehingga regangan itu selalu berada di bawah batas maksimum leher atau tungku penyaringan, tidak lain hanyalah satu ruang pemanasan yang dirancang dengan baik dimana laju pendingin dapat diatur sehingga memenuhi persyaratan.
d. Penyelesaian
Semua kaca yang sudah disangai harus mengalami operasi penyelesaian yang relative sederhana tetapi sangat penting. Operasi ini menyangkut hal-hal sebagai berikut:
- Pembersihan
- Penggosokan
- Pemolesan
- Pemotongan
- Gosok-semprot dengan pasir
- Pemasangan email klasifikasi kualitas
- Pengukuran
Reaksi Kimia Yang Terjadi Selama Proses Pembuatan
Reaksi kimia yang terlihat dalam pembuatan kaca dapat diringkas sebagai berikut (Austin, dkk. 2005) :
Na2CO3 + aSiO2 → Na2O.aSiO2 + CO2
CaCO3 + bSiO2 → CaO.bSiO2 + CO2
Na2SO4 + cSiO2 → Na2O.cSiO2 + SO2 + SO3 + CO
Reaksi yang terakhir ini dapat berlangsung seperti pada persamaan berikut (Austin, dkk. 2005) :
Na2SO4 + C → Na2SO3 + CO
2Na2SO4 + C → 2Na2SO3 + CO2
Na2SO3 + cSiO2 → Na2O.cSiO2 + SO2
- Penggosokan
- Pemolesan
- Pemotongan
- Gosok-semprot dengan pasir
- Pemasangan email klasifikasi kualitas
- Pengukuran
Reaksi Kimia Yang Terjadi Selama Proses Pembuatan
Reaksi kimia yang terlihat dalam pembuatan kaca dapat diringkas sebagai berikut (Austin, dkk. 2005) :
Na2CO3 + aSiO2 → Na2O.aSiO2 + CO2
CaCO3 + bSiO2 → CaO.bSiO2 + CO2
Na2SO4 + cSiO2 → Na2O.cSiO2 + SO2 + SO3 + CO
Reaksi yang terakhir ini dapat berlangsung seperti pada persamaan berikut (Austin, dkk. 2005) :
Na2SO4 + C → Na2SO3 + CO
2Na2SO4 + C → 2Na2SO3 + CO2
Na2SO3 + cSiO2 → Na2O.cSiO2 + SO2